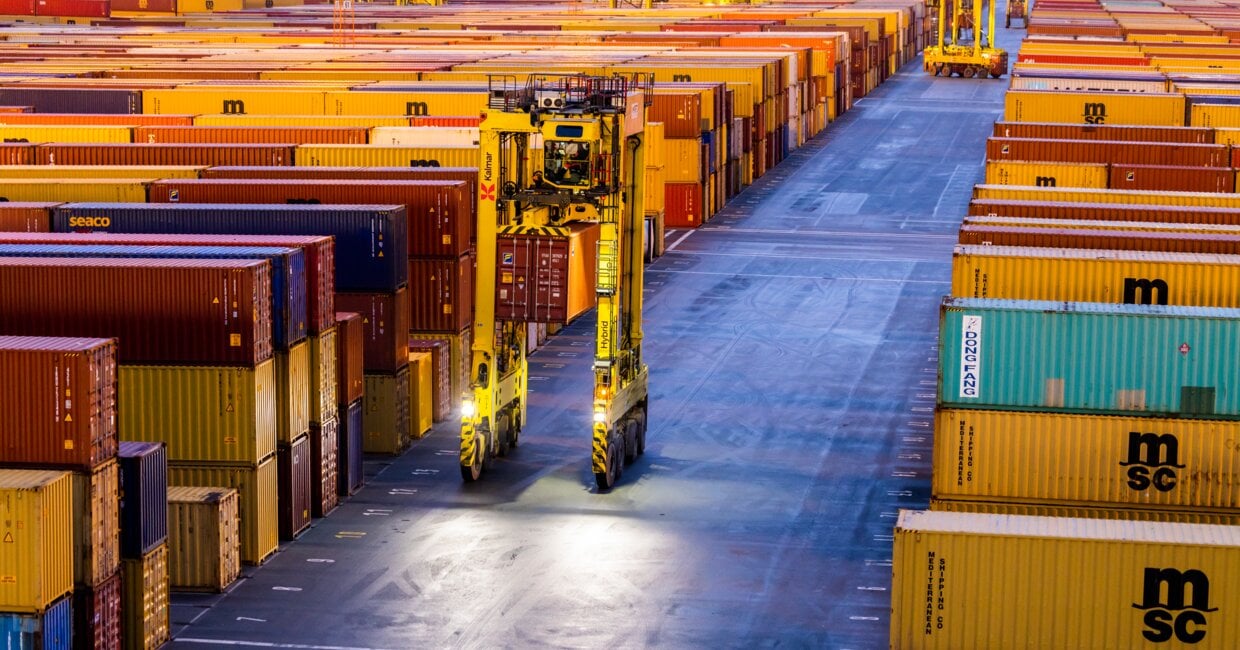
Straddle Carriers for container handling: What you need to know
Key Takeaways
- Straddle carriers are one of the most common types of vehicles used for handling containers.
- Unlike traditional trucks, a straddle carrier carries its load under the frame of the vehicle.
- Straddle carriers enable better performance for container cranes by decoupling their operations from horizontal container transportation.
- Straddle carriers allow terminals to handle all container movement tasks and stacking with a single type of machine.
- The current standard for straddle carriers is hybrid drive, but battery-powered machines are gaining in popularity.
- Straddle carriers are available as both manually driven and fully automated versions.
Introduction
Since the 1970s, straddle carriers have been a standard type of equipment at container ports and terminals around the world. Thanks to their flexibility, efficiency and cost-effectiveness, straddle carriers are a mainstay of container handling and are expected to continue in this role for the foreseeable future. This article analyses the straddle carriers used for stacking and moving shipping containers at port terminals and intermodal yards. We review the basics of straddle carriers along with their key features and benefits. To avoid possible confusion with other types of machines, this type of straddle carrier is often called "Portalhubwagen" or "Van Carrier" in German, "carretilla pórtico" in Spanish, and "konttilukki" in Finnish.
What is a straddle carrier?
A straddle carrier is a freight-carrying vehicle that carries its load underneath its frame instead of on top like a conventional truck. This allows the straddle carrier to load and unload containers or other cargo without the assistance of cranes or forklifts, making it a highly efficient solution for container terminals.
Straddle carriers are typically used at ports and terminals, as well as in intermodal yards. The most common usage application for straddle carriers is container handling. The ability to straddle the load provides greater stability and control for the machine, making straddle carriers a preferred choice for many industries.
At container terminals, one of the most significant benefits of straddle carriers is that they enable the decoupling of container movements at the quay and landside parts of the terminal. As containers can be placed on and picked up from the ground, ship-to-shore and yard cranes do not need to wait for horizontal transportation equipment and can therefore operate continuously at maximum productivity.
Straddle carriers are the only type of container handling machine that can handle all container moving tasks in the terminal, from serving ship-to-shore and yard cranes, to loading and unloading road trucks and even stacking containers up to four high in the yard. Smaller versions of the straddle carrier, known as straddle carriers for shuttle operations, are designed for use primarily as horizontal transportation and feature a lower 2-high stacking capacity.
How do straddle carriers work?
Straddle carriers operate by straddling their load and lifting it underneath the vehicle using a lifting apparatus. The driver operates the machine from a cabin on the top frame without needing to leave the vehicle for loading and unloading.
The lifting mechanism of a straddle carrier consists of hydraulic or electric-powered spreaders that can adjust to the size of the container being lifted. The spreaders grip the load securely at the twistlock fittings at the corners of the container, allowing the machine to lift and transport the container safely. The driver's cabin is designed to provide a clear view of the load and surrounding area, which enhances safety and precision during operations. When the straddle carrier is fitted with an extendable twin-lift spreader, two 20-foot containers can be handled simultaneously.
Modern straddle carriers are equipped with advanced drive and steering systems for enhanced maneuverability. When required, the machines are can move diagonally in "crab" mode or even pirouette on the spot, enabling shorter work cycles and increased efficiency.
Straddle carriers have traditionally been diesel-electric powered, but the current industry standard for new machines is hybrid drive. Compared to traditional diesel-electric machines, hybrid straddle carriers can reduce emissions by up to 40% by using regenerative power systems coupled with highly efficient diesel engines that use less fuel. Fully electric straddle carriers are also rapidly gaining popularity as terminal operators seek to reduce their emissions and CO2 footprints.
From the early 2000s, straddle carriers have been available as automated versions. The first fully automated Kalmar AutoStrad™ terminal was the Patrick Container Terminal in Brisbane, which began operations with 27 machines in 2006. Since the introduction of the system, the terminal has become known as one of the safest in the world.
Where are straddle carriers commonly used?
Straddle carriers are widely used at ports and terminals around the world for handling ISO standard shipping containers. Sites operating straddle carriers include many of the world's largest and most advanced container terminals, such as ECT Delta in Rotterdam, Patrick Terminals in Australia and TraPac in Los Angeles. Many leading terminal operators are currently extending their existing straddle carrier fleets with hybrid and/or electric machines.
Examples of straddle carrier customer cases at container terminals include:
Medcenter Container Terminal (MCT), Italy
In 2025, Kalmar signed an agreement with Medcenter Container Terminal (MCT) to supply 20 Kalmar hybrid straddle carriers. The significant order was booked in Kalmar’s Q4 2024 order intake, with delivery of the machines expected to be completed during Q1 2026. MCT is located in the southern Italian port of Gioia Tauro and handles approximately 4 million TEUs (Twenty-foot Equivalent Units) of container cargo annually. Kalmar has delivered over 200 straddle carriers to MCT since 1995.
APM Terminals, Tangier, Morocco
In late 2024, Kalmar concluded an agreement to supply APM Terminals in Tangier, Morocco with a further 20 Kalmar hybrid straddle carriers. The units will be deployed at APM Terminals MedPort Tangier. Opened in 2019, APM Terminals MedPort Tangier is a transshipment terminal located at the Tanger Med 2 port complex. Tanger Med 2 currently operates a fleet of 65 Kalmar straddle carriers.
GMP, Le Havre, France
In Le Havre, France, Générale de Manutention Portuaire (GMP) has been using Kalmar straddle carriers since the early 1990s and has ordered a total of 54 hybrid units since 2020. In 2024, the terminal signed its latest order for 26 new hybrid straddle carriers from Kalmar.
DP World Southampton, UK
Leading logistics management services company DP World is committed to reducing and mitigating the carbon footprint of its operations through reduced energy use and product designs that help cut greenhouse gas emissions. In 2024, Kalmar announced an order for an additional 14 hybrid straddle carriers at DP World's container terminal in Southampton. DP World Southampton has operated Kalmar straddle carriers since 2007, and the latest order brought the total number of Kalmar straddle carriers at the terminal to 82. Hybrid straddle carriers significantly reduce both the fuel consumption and CO2 emissions of straddle carrier operations at the terminal compared to traditional diesel-powered machines.
DP World London Gateway, UK
In London, DP World operates a semi-automated container terminal with 78 Automated Stacking Cranes served by a fleet of 49 Kalmar straddle carriers. The machines include automation-ready diesel-electric and hybrid models as well electric straddle carriers. The fleet will be further augmented by the delivery of 12 additional Kalmar Electric Straddle Carriers in 2026.
Hutchison Ports ECT Delta, Rotterdam, Netherlands
In the Netherlands, Hutchison Ports ECT Rotterdam (ECT) uses its fleet of straddle carriers for loading and unloading trucks on the land side. In 2024, Kalmar concluded an agreement to supply Hutchison Ports with two fully electric and eight hybrid straddle carriers for its ECT Delta terminal. The new straddle carriers are part of a fleet renewal programme that will support the goal of ECT to achieve emission-free operations at its ECT Delta and ECT Euromax terminals by 2035.
Patrick Terminals, Australia
In 2023, Kalmar announced an agreement to supply ten new Kalmar hybrid straddle carriers to Patrick Terminals in Melbourne. Patrick Terminals is Australia's leading container terminal operator, handling over three million TEUs annually. The company operates some of Australia's most technologically advanced terminals at four strategically located ports, including the Kalmar AutoStrad™ terminals in Brisbane and Sydney.
APM Terminals Pier 400, Los Angeles, USA
In Los Angeles, APM Terminals' Pier 400 facility runs a fleet of 132 Kalmar AutoStrads™ and is currently piloting three fully electric AutoStrads™ as a step towards electrification. The site is one of the world's most advanced automated container terminals, handling over 1.5 million container moves in 2024.
TraPac, Los Angeles, USA
At TraPac in Los Angeles, which is both a marine and intermodal terminal, 40 Kalmar automated straddle carriers feed the terminal’s 29 Kalmar Automated Stacking Cranes, as well as operate an additional stacking yard for containers.
(Image: Kalmar automated straddle carriers move containers at TraPac Los Angeles.)
What are the advantages of using straddle carriers?
Straddle carriers offer numerous advantages for container terminals, most notably the possibility of separating crane movements and horizontal container transportation from each other, and the ability to handle all container moving tasks with a single type of machine. Straddle carriers are an extremely versatile and cost-effective solution that enables container handling capacity to be assigned wherever it is needed at the terminal. This flexibility makes straddle carriers particularly useful for terminals with limited space and/or irregularly shaped stacking layouts.
Straddle carrier key benefits:
- Decoupled Operations: Straddle carriers enable decoupled crane operations by allowing cranes to operate independently of container movements. This increases the efficiency of crane operations and reduces idle time, leading to higher overall productivity.
- Flexibility: Unlike heavy yard cranes, straddle carriers can be flexibly assigned to landside or quayside operations, or redeployed to another area of the terminal based on capacity requirements and vessel schedules.
- Enhanced Efficiency: With a single type of machine handling all horizontal transportation, straddle carriers streamline the movement of containers and help minimize ship and truck turnaround times.
- Space Optimization: With their flexible stacking capabilities, straddle carriers maximize the use of available yard space, allowing terminals to handle more containers within the same area. This is particularly important where space is limited or when the terminal site is of an irregular shape.
- Cost-Effective Operations: By reducing reliance on multiple types of equipment, straddle carriers help lower operational costs. They eliminate the need for additional cranes and horizontal transportation equipment, resulting in significant cost savings for businesses.
- Improved Safety: Straddle carriers are designed to handle heavy loads safely, reducing the risk of accidents. Automated straddle carriers enhance terminal safety even further by keeping people out of the operating area of heavy equipment.
- Environmental Benefits: Modern straddle carriers are equipped with eco-efficient features such as hybrid or battery-powered power systems. These features help reduce carbon emissions and align with global sustainability goals.
What are the load capacities of straddle carriers?
The load capacities of straddle carriers vary by model and manufacturer. Kalmar straddle carriers can handle loads ranging from 40 to 60 tons depending on the specific configuration. When fitted with twin-lift spreaders, container straddle carriers can lift two 20-foot containers simultaneously. Current hybrid and electric straddle carriers are designed to provide the same lifting capacity as their diesel counterparts while offering additional environmental benefits.
What are the key features of straddle carriers?
Modern straddle carriers are equipped with several key features that enhance their performance and efficiency, including maneuverability, 4-high stacking, automation readiness and advanced safety features. Hybrid and battery drive help cut down on on-site emissions to support terminals in meeting their sustainability goals.
Straddle carrier key features:
- High Maneuverability: Straddle carriers are designed to operate efficiently in confined spaces, making them ideal for crowded terminals. The ability to move diagonally in a "crab" mode or pirouette on the spot provides greater flexibility and reduces the time required for container handling.
- Stacking Capabilities: Straddle carriers can stack containers up to four high, optimizing yard space and enhancing operational efficiency. This feature is particularly valuable at terminals with limited space and/or irregular layouts.
- Automation and Connectivity: Modern straddle carriers are equipped with advanced guidance systems and data connectivity, enabling real-time monitoring and precise operations. These features allow for remote control and monitoring, reducing the need for manual intervention and improving overall efficiency. Fully automated straddle carriers are also available for terminals seeking to increase their level of automation.
- Eco-Friendly Options: Hybrid or battery-powered straddle carriers reduce carbon emissions and help terminal operators align with their sustainability goals. These eco-friendly options support terminals in meeting their stakeholder requirements and reducing their environmental impact.
- Advanced Safety Features: Straddle carriers are equipped with various safety features, including collision avoidance systems, load monitoring, and emergency stop mechanisms. These features enhance the safety of operations and reduce the risk of accidents.
- Ergonomic Design: On modern straddle carriers, the driver's cabin is designed for comfort and ease of use, with adjustable seats, climate control, and intuitive controls. This ergonomic design helps reduce operator fatigue and improve overall productivity.
(Image: Kalmar Electric Straddle Carriers opearting in Gdynia, Poland.)
What are the limitations of straddle carriers?
While straddle carriers offer numerous benefits, they also have some specific features and requirements that need to be considered when planning equipment fleets and designing terminal operating concepts. Straddle carriers are a technically advanced solution that requires a somewhat higher investment than other horizontal container transportation concepts, and they also need more planned maintenance to ensure they operate optimally. Straddle carriers also require drivers with specialized training, which may be a challenge for terminal operators in some markets.
- High Initial Cost: The initial investment for purchasing straddle carriers can be relatively high compared to simpler horizontal transportation equipment such as Automated Guided Vehicles (AGVs). The cost of acquiring and deploying a fleet of straddle carriers, especially advanced models with automation and eco-friendly features, can be significant.
- Stacking Density: Although straddle carriers are able to achieve relatively high stacking densities when used for managing the container stack in the yard, for terminals that require the highest possible number of containers per unit of land area, other solutions such as Automated Stacking Cranes (ASCs) may be preferable.
- Maintenance Requirements: Straddle carriers require regular maintenance to ensure optimal performance, which can add to operational costs. The complexity of the lifting mechanism and control systems means that specialized maintenance is often required. For automated straddle carriers, the maintenance requirements are even more demanding.
- Limited Speed: Straddle carriers travel at relatively low speeds, which may not be ideal for all applications. While they are highly efficient for short-distance transport within terminals, they may not be the best choice for long-distance transport.
- Space Requirements: Despite their manoeuvrability, straddle carriers still require a certain amount of space to operate effectively. In areas with extremely limited space, other types of equipment may be more suitable.
- Operator Training: Operating a straddle carrier requires specialized training and skills. Ensuring that operators are properly trained and certified can add to the overall cost and complexity of implementing straddle carriers.
Conclusion
Straddle carriers are a versatile and efficient solution for handling large and heavy loads at container terminals. Their unique design, advanced features, and ability to operate in confined spaces make them an essential asset for port terminals, intermodal yards, and other industries. By understanding the key features, advantages, and special requirements of straddle carriers, businesses can make informed decisions about whether to invest in this technology. With ongoing advancements in automation, connectivity, and eco-friendly options, straddle carriers are likely to continue playing a crucial role in the future of container handling and logistics.
相关文章
订阅我们的刊物
订阅我们的出版物